Implementing Regenerative Design: Paul Hutton Q&A
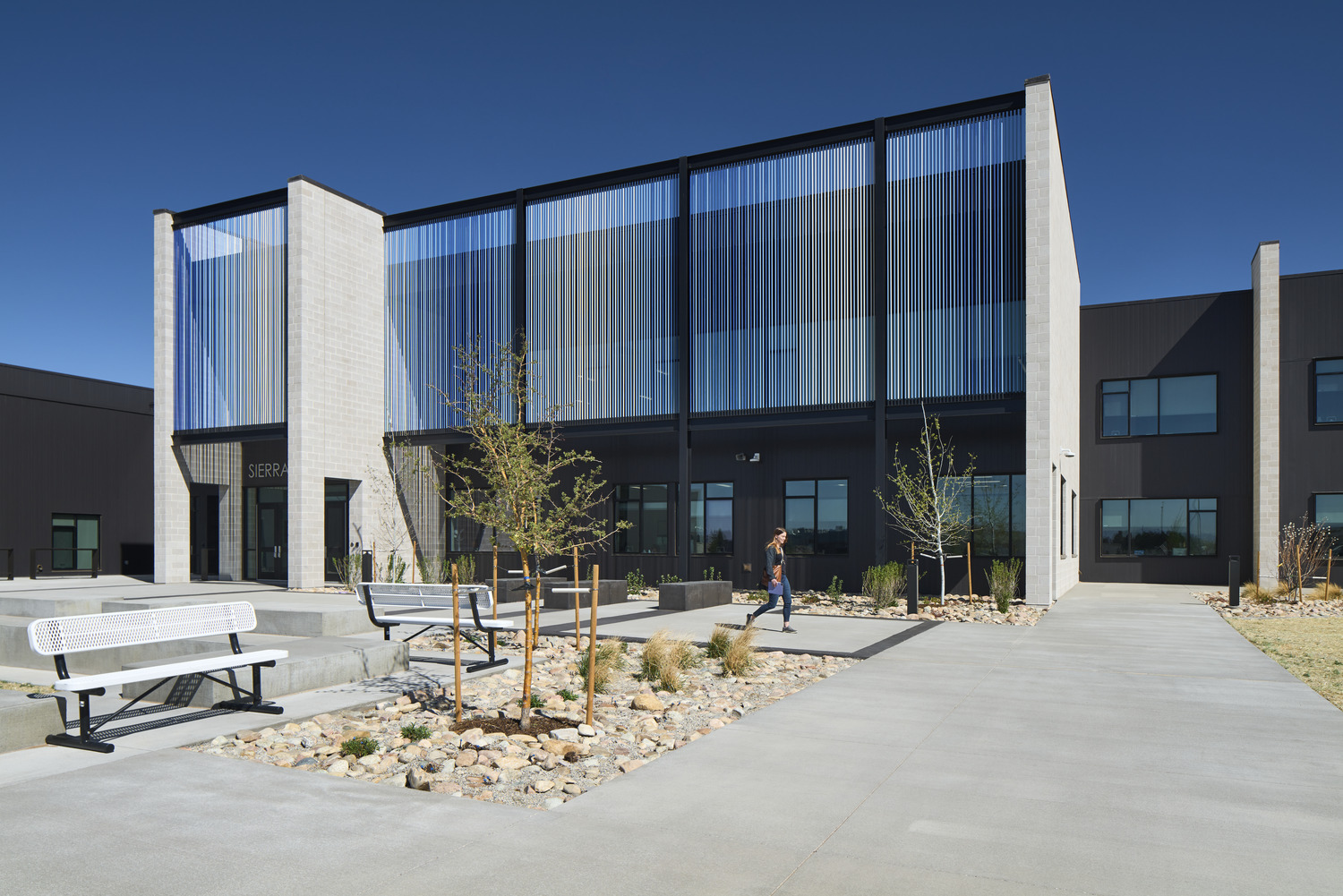
Cuningham’s Paul Hutton recently sat down with Connect CRE reporter Amy Wolff Sorter for a two-part Q&A on the application and implementation of regenerative design. Highlights from that interview are below. Check out the full piece here.
Connect CRE: How does regenerative design differ from sustainability?
Paul: The difference between sustainability and regenerative design is an evolution of thinking. Where sustainability meant “do less harm,” the regeneration paradigm is “restore the planet.”
Before going on, it’s important to note that sustainability has achieved a lot of good, especially in terms of energy efficiency. According to Architecture 2030, while building area in the U.S. has greatly increased, the energy used by those buildings has decreased. We succeeded in decoupling floor area and energy use. But sustainability stops being effective at the point where repair and restoration becomes necessary, which is where the world is now.
Interest in sustainability is worn out. LEED registration is a proxy for interest, and in recent years we’ve seen what can only be described as “LEED fatigue.” New certifications declined from 8,425 in 2015-2016 to 1,472 in 2018-2019. The LEED system is being re-tooled to reflect a more regenerative approach and I think that’s a great thing.
Connect CRE: Is regenerative design more expensive than other environmental tools?
Paul: I think that depends on your point of view. If the goal of a regenerative design-based project is to “do good” and restore environments on a holistic basis, then one must consider not just the immediate expenses of the building materials and methods used to create the structure, but also the long term financial, environmental and social benefits that will accrue because of the building.
It’s true that certain aspects of regenerative design may have higher upfront costs; net-zero energy and water require things traditional buildings don’t need. Reducing embodied carbon may mean sourcing material from a more expensive vendor. But in the long run, when you factor in the recapture of lost natural space, the reduction of waste, and potential impact on reversing climate change, regenerative design costs should be seen as spectacularly cheaper than how we’ve built things in the past.
Connect CRE: You mention the circular economy as an important part of regenerative design. What is it and how does it work?
Paul: The circular economy represents a different way to think about how we relate to the world. In our current, linear economy, we take raw material from nature like rock and ore. We convert it into a resource like cement or steel, and then. Then at the end of that product or building’s life cycle, it becomes waste. Even though some that waste is recycled, this linear process is becoming impossible to continue as we’re running out of natural resources.
In the circular economy, the idea is that waste – the end-of-life state in the linear system – is continuously turned into something new. Waste is designed out of the system entirely.
The circular economy has five key principles: Circular Supply, Resource Recovery, Life Extension, Sharing Platforms, and Product as Service. The circular economy doesn’t operate separately from the current economy, it requires participation, particularly from our industry. We are the primary decision makers on materials, their use and reuse and construction methodologies.
As it relates specifically to development of the built environment, Cuningham has developed a publicly available online toolkit that allows developers to learn about the circular economy. It also lets them take a closer look at their projects to see how to incorporate the ideas into their designs.