From Bits to Bolts
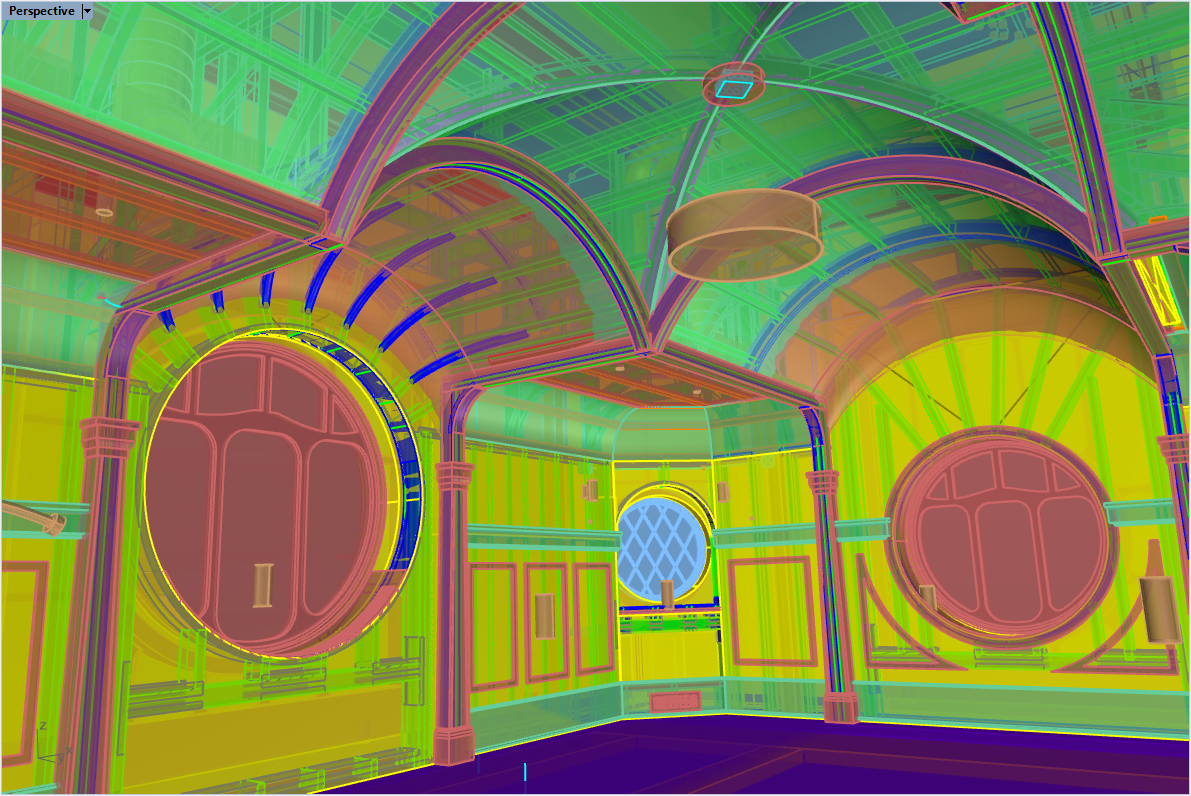
Direct Fabrication Techniques Save Time, Effort, and Money for Complex Projects
The use of digital production tools in architectural design provides practically limitless freedom in designing complex and organically-shaped spaces. However, without a clearly defined process, this complexity can leave stakeholders nervous about financial and time impacts on a project.
Cuningham recently had the opportunity to explore a direct fabrication processes on a themed tenant improvement project and found that direct fabrication can save time, money, and effort while delivering the complex and beautiful shapes promised by modern digital tools. For these benefits to be realized, it is important to develop and share a clear process to all stakeholders. We happily share ours below.
Developing the Design
From the start, we knew our project would incorporate forms that traditional metal framing subcontractors have difficulty producing in the field, including groin vaults and curved corridors with circular cross sections. In addition, these forms needed to incorporate Mechanical, Electrical, Plumbing, and Fire Protection (MEPF) elements, as well as specialty office infrastructure (including wireless internet, public address systems, and extensive low voltage wiring). To get this complex assembly right, we needed to have all elements designed long before the framing was in place. After careful consideration, we elected to pre-fabricate as much as possible to avoid field errors compounding into expensive clashes.
Using digital modeling tools, we first designed the form of our space, then offered model access to our MEPF consultants using industry-standard cloud software. Weekly clash detection meetings allowed the general contractor to align all stakeholders on each design decision and ensured that the high density of MEPF items were properly vetted against client-driven design changes. This near-constant communication proved invaluable throughout the life of the project, and we owe a lot of thanks to the contractor JP Cullen for organizing such a complex process.
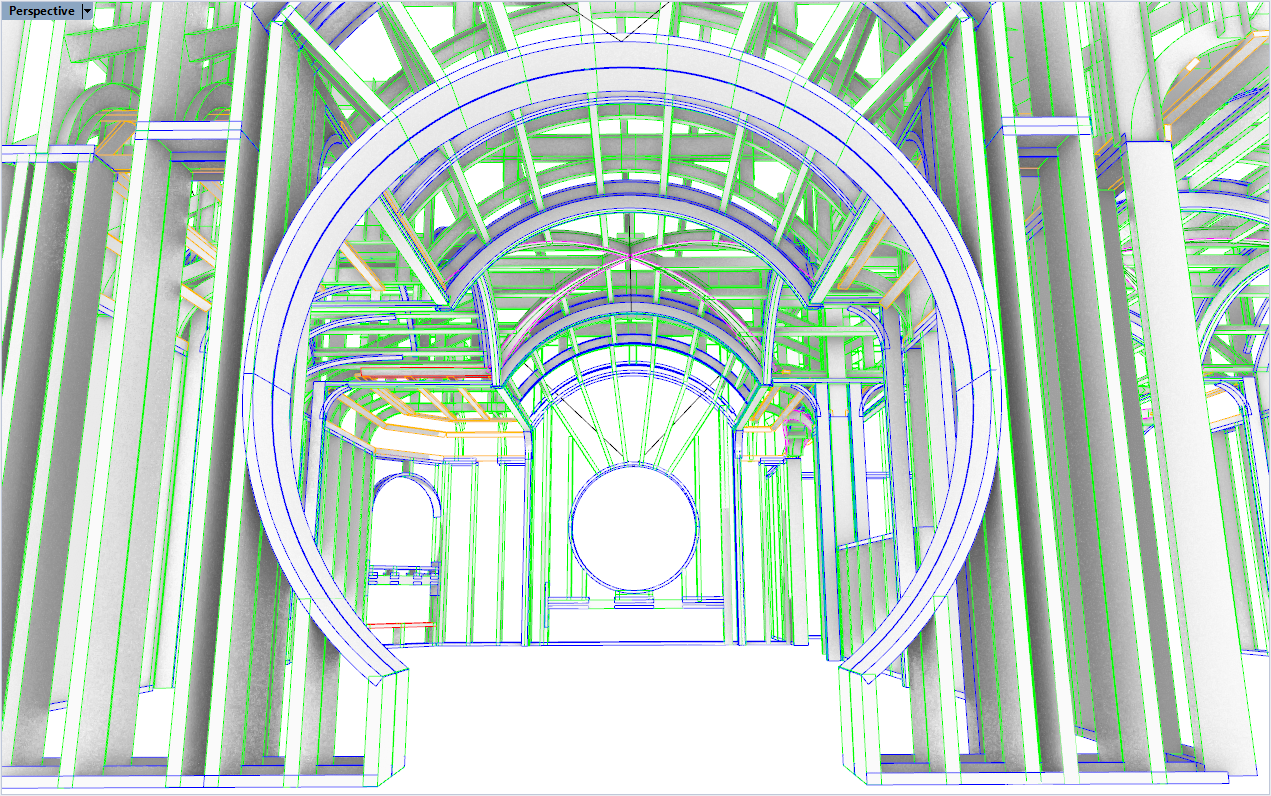
Direct Fabrication Planning
As the design of the space stabilized, we sought out a partner that could produce the complex forms we needed while being able to keep up with our fast-moving design teams. We were delighted to find that Radius Track – an industry leader in providing light-gauge steel systems via direct fabrication – was headquartered within our city. We brought them on board the project team and gave them access to the very same model used for our design and clash detection. This meant that they were able to see design changes in real-time and react immediately, ensuring that there were no issues integrating systems or design elements.
Once the design had been fully approved and all trades fully coordinated, we made use of the blockchain-secured signature tool Concert to sign off on the final design and provide security to the prefabricator that they were getting a final model that could not be altered after the fact without their knowledge. This final approved surface model is key to setting the rules for installation, so ensuring its accuracy was critical to us and the prefabricator. From there, they could begin the manufacturing process knowing that all stakeholders had agreed and verified the final product.
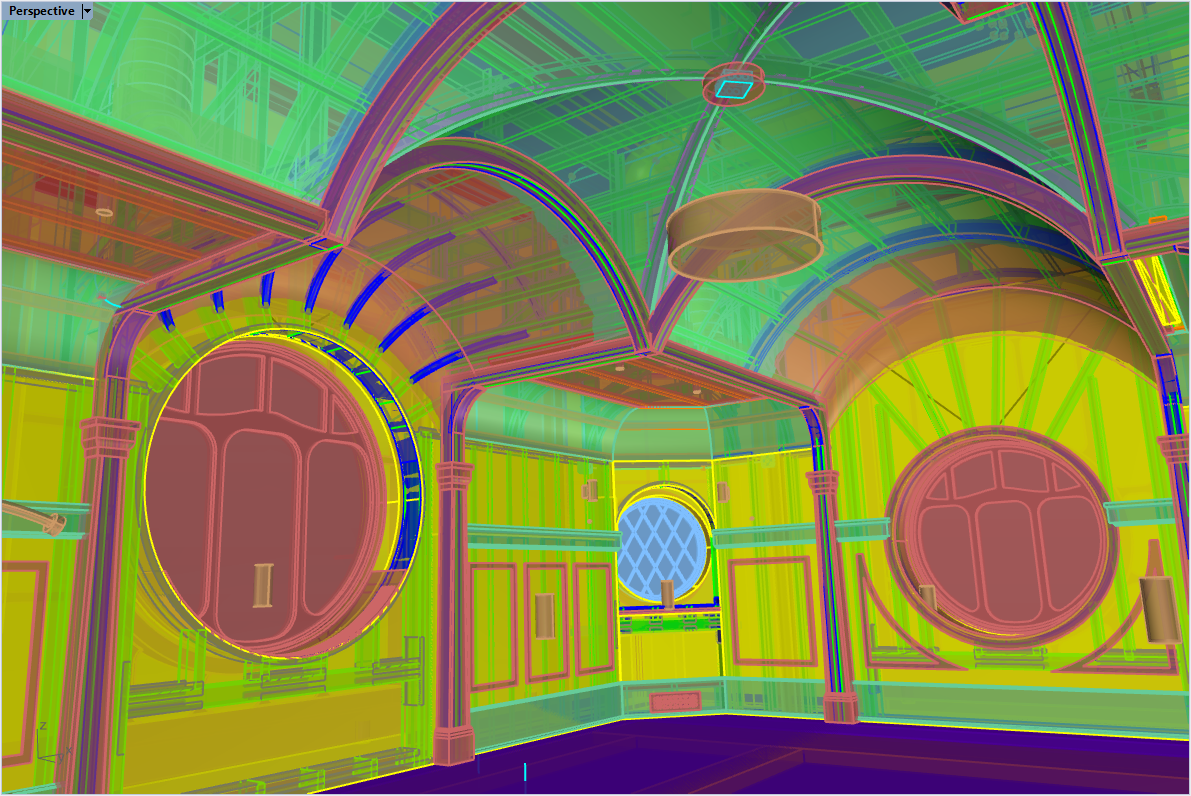
Production and Assembly
To begin the process, Radius Track took our surface model and produced their own digital model that included each individual framing element modeled to a tolerance of 1/8”. This formed the input for their proprietary machinery to create each framing element but had the added benefit of being placed within our building model, allowing each trade to verify the location of their systems down to the individual stud.
As the design team continued refining to the reality of the in-wall steel, the fabricator began bending and assembling the individual pieces and sequenced panels required for our design. This process took about six weeks for the roughly 1,250-square-foot space, and care was taken to time this fabrication with the exterior work so that efforts on the interior could begin simultaneously and without delay. Once completed, the panels were flat packed and shipped to the job site, then assembled by the contractor’s subcontractor using detailed installation drawings provided by the fabricator. This entire process went smoothly, and even accommodated significant client-driven design changes with minimal interruption. Construction proceeded with no significant clash issues, and the client was beyond thrilled with the completed space.
Lessons Learned
The process of direct fabrication for complex interior environments is one we would participate in again with no hesitation. We saw significant savings in time, cost, and effort required to produce a unique space for our client. Most importantly, they were impressed by the results!
However, there are many considerations to keep in mind when ensuring positive outcomes for the project. First, all collaborators must be comfortable working in a cloud-based digital model and must be able to produce models that are well-detailed and dimensionally-accurate while also meeting design intents. The General Contractor must be comfortable in this environment and take an active role in laying out the project in a 4D manner, knowing where — and more importantly when — each piece will fall into place. All collaborators need to feel secure in the knowledge that every model element is finalized and won’t be modified without their knowledge. Because of this, verifying model integrity through Concert was important to our team. Finally, it is important for the architect to be aware of the fabricator’s output so that they know what can and cannot be changed after the manufacturing process and guide the client and consultants accordingly.
Thanks to our forward-looking partners and model-first delivery policy, we were able to use the above steps to produce a space that the client absolutely loved without ever printing a single sheet of design documents!
written by Dan Dolan